In the course of ongoing solar panel pricing battles and sharpening import tariffs in the important US and EU markets – exercising enormous pressure on solar panel manufacturers in China .
SinoVoltaics observes bizarre and hefty business demeanors among some manufacturers in China, ever ready to increase profits and keep cash flowing at all means. Read about it in this first part on PV quality fraud.
In this turbulent situation, importers of solar panels (and other PV products) face multiple threats to their businesses from such black sheeps in form of fake performance data, non-existing certifications, useless warranties and other examples of obscure and damaging business behaviour.
In this threepart article series, SinoVoltaics will draw from these experiences and observations outline what importers of solar PV panels shall bear in mind and take care of.
A] Fake Electroluminescence (EL) and flash test data
When purchasing solar panels from China, importers are usually provided flash test data of all panels purchased.
Yet, only few customer also ask for EL images of their panels. However, the data from black sheep companies do in no way mirror the real performance.
As fake El and flash test data is a broader and complex issue, following are the major problems and cheat-challenges customers should be aware of:
1) Unawareness about various flash testing device quality classes.
According to IEC 60904-9:2007, flash test machines are classified into different quality classes depending on following three quality factors (classified each into A-C quality range).
These are: spectral alignment to AM 1.5 (A: -/+ 25%, B: -/+ 40%, C: -60% to 100%), non-uniformity of irradiation intensity (A: 2%, B: 5%, C: 10%) and long-term stability of irradiation intensity (A: 2%, B: 5%, C: 10%).
As even slight deviations in irradiation intensity have a big impact on the performance of a solar panel, it is therefore necessary to obtain quite precise test data – optimally measured with equipment of AAA quality.
2) Only focus on flash test data lists.
Flash test lists mostly provided in Excel format can be manually calculated and edited; such fake test data attempts are not uncommon.
To verify the genuineness of the provided flash test data, the manufacturer shall also provide I-V curve images for each panel to verify compliance with test data.
3) Mal-calibration of flash tester.
Flash test machines are before testing to be calibrated to a standard panel (golden panel) certified by a recognized certification body.
Calibration should be in accordance to the standard panel’s output data in order to avoid sugarcoated data in favor of a manufacturer’s goods.
4) Fake EL test images.
Analyzing EL test images requires not only analytical know-how, but also high concentration and good eyes and can thus be quite tiring.
The clever black sheeps among the manufacturers in China, aware about the B or even C-grade quality of their cells and quality defects such as cell cracks, shunts, finger defects, inactive cell (parts), dark spots etc. and other cell-inherent problems in their panels, assemble a range of good EL test images from the good batches of an order and multiply these test images – assigning each a separate serial number from the order list.
In many cases, the manufacturer can count on the fact that the customer does neither own EL testing equipment nor understands the features of various cell-inherent defects.
For the untrained eye, it is also difficult to differentiate the images and find such cheats.
To obtain genuine test data it is therefore recommended to conduct EL testing on-spot at the factory.
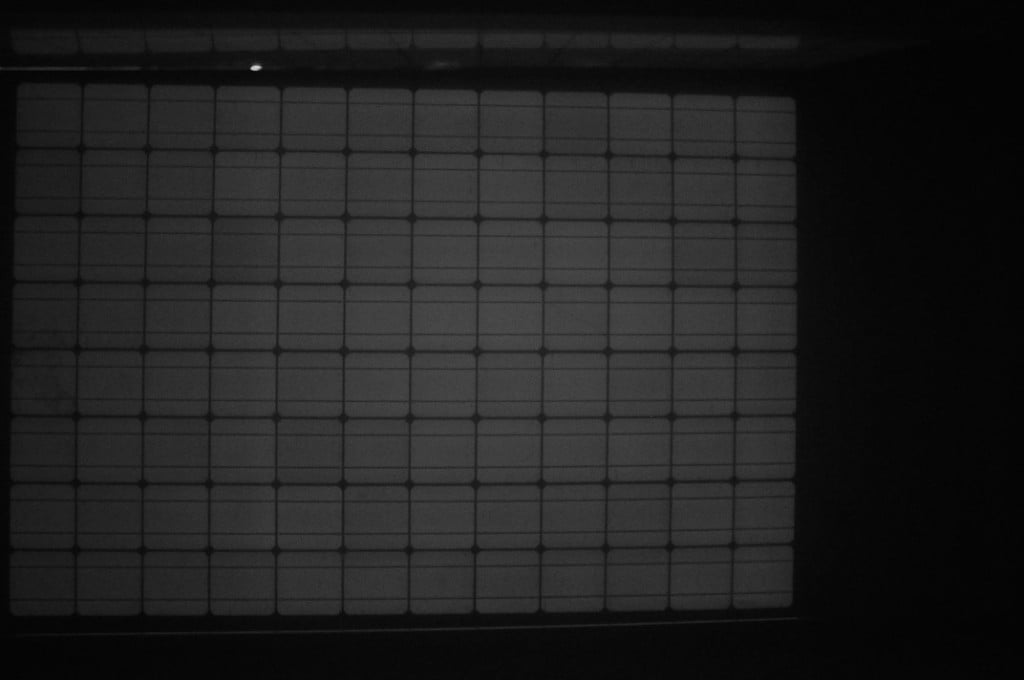
Dark EL (Electro luminescence)
5) Overly dark EL test images.
EL images of a panel are obtained by feeding current into the cells and radiative recombinations of carriers cause light emission.
The longer the “snapshot” time is (ideally at 10s), the clearer becomes the EL images revealing ever more details about defects in cell.
Nevertheless, unaware customers can be easily trapped by being provided dark EL images.
Solution: have professional PV quality experts on site properly calibrating the testing devices, verifying the genuiness of the flash test and EL data and conducting thorough analysis of test data
B] Forged shipment lists
It has been common practice for many solar manufacturers in China – not only the large ones – to counter production capacity problems or meet a certain target price via subcontracting.
In an often recurring form of this procedure, factory A sells the panels at a negotiated pricing to the importer overseas and handles the production work to factory B.
Factory A adds a profit margin, does not disclose the client’s details to factory B and claims in front of the client these panels to be own production, thus keeping the client.
Generally, factory B is carefully picked and instructed to meet factory A’s quality requirements.
Sinovoltaics’ observations have shown that there are customers that – if finding out – not only are unhappy about this demeanor, literally paying unnecessary extra money to factory A, but are also understandbly concerned about potential quality issues and useless marketing promises if honestly referring to factory B as the product’s source.
The issue of subcontracting is quite rampant among Chinese solar manufacturers and may in certain cases pose quality problems.
If undisclosed to a client, a situation which is not rare, it amounts to a certain degree of brand cheating.
The solar PV quality inspection company Sinovoltaics has experienced cases during which during inspection and audits at the factory on-site the true source of the goods had been revealed.
Solution: to avoid unwanted subcontracting, check production factory on-site and its relation with the source of purchase (factory A).