Solar panels undergo a long multi-step, time- and raw material-consuming process until they are ready to be sold.
As a globalized industry with still most of the production of solar panels taking place in East and Southeast Asia and the largest share of end consumers being geographically distant from the manufacturing origin, these valuable goods must also be shipped over a long distance via ocean.
Being high-priced products, an important – yet often neglected aspect in the solar industry – is the significance of correct, safe, and efficient packaging of the solar panels.
Solar panels reaching the customers broken, cracked, deformed, or scratched as a result of improper packaging are not only annoying but also costly. With panels having left the factory in good quality conditions but being damaged on the way, claims and disputes may come up quickly. This brief article is an introduction to solar panel packaging.
Solar panel Packaging basics
Solar panels are typically either horizontally or vertically stacked in a box. Usually, separators are placed between each module, and extra protections are added to the four corners of each module stack. In some cases, modules are also packed in individual cartons boxes to be packed into a large master carton box.
The box on the pallet is then sealed and strapped followed by being wrapped in plastic film. Solar panels are then usually shipped via ocean on pallets, holding on average 28-30 panels and – depending on order quantities, with extra few panels stacked on top in extra small cartons.
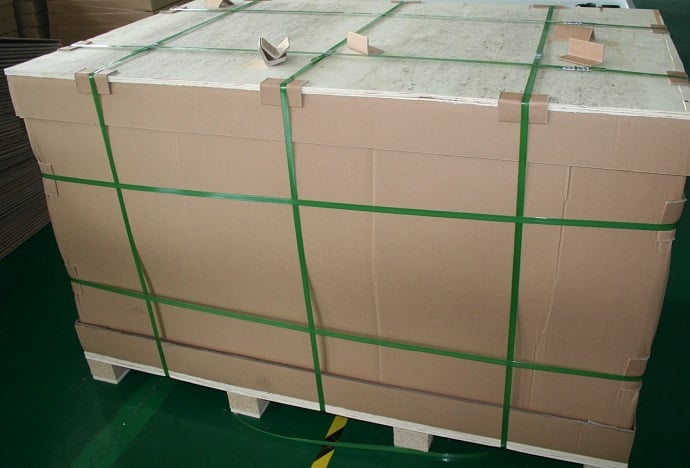
Strapped pallet with solar panels
This reference to ‘typical’ packaging and shipping underlines, that there is globally no accepted and widely applied standard about the packaging, loading, transport, and unloading of solar (PV) modules.
The big hurdle to establishing a globally followed standard is the varying client requirements from manufacturers, different solar panel products, and lastly a lacking overall willingness by many manufacturers to deviate from their own packaging philosophy, particularly since the packaging is a way to cut costs and corners in a heavily embattled industry, saving on packaging material and qualified packaging personal.
Problems of bad packaging
Horizontally stacked each on top of each other can cause stresses on the panels below that can lead to defects clients do not detect for a long time, especially micro-cracks that even grow and show their detrimental impacts after time only.
Packed horizontally, the solar panels are usually separated with either carton or plastic separators. Most available separator solutions are not of great help when it comes to protecting the module from mechanical stresses.
The carton separators and also many available plastic separators are not strong and wide enough to sufficiently separate the modules from each other, thus the upper layers of the stack cause weight stress towards the lower layers. The stiletto effect occurs then with several hundreds of kilograms pressing on the corners of the bottom panels which can lead to micro-cracks in the cells.
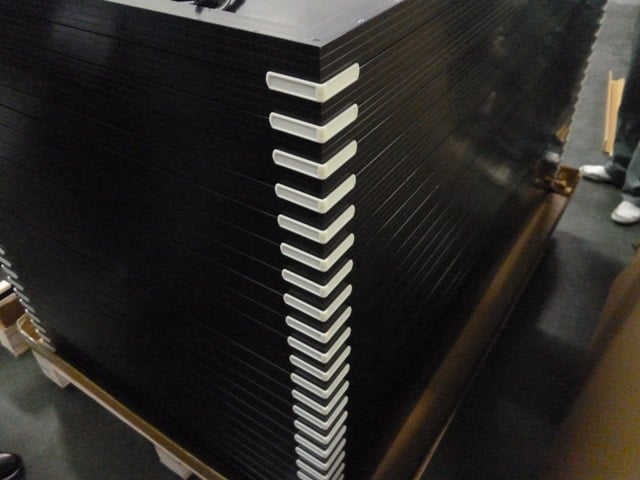
Horizontal packaging with plastic separators
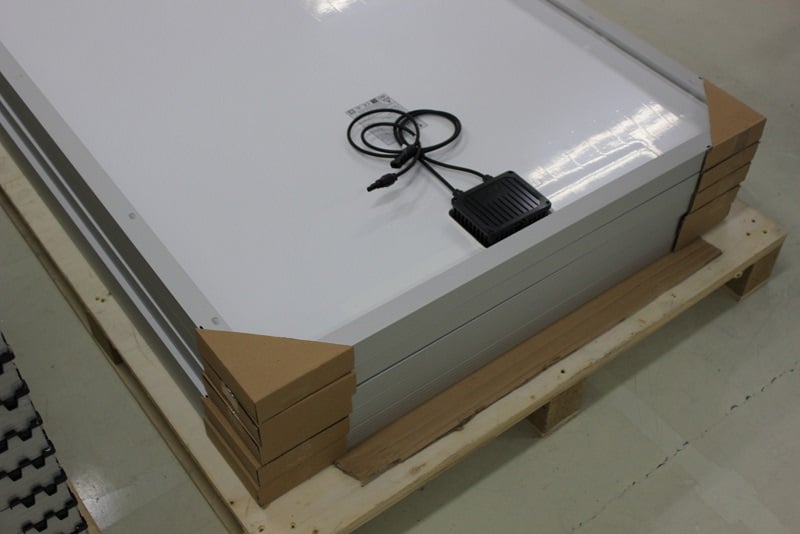
Horizontal packaging with carton separators
With such potential occurrences of mechanical and weight stresses, it is usually a preferred and better solution to pack the panels vertically to minimize top-to-bottom pressure and weight stress to the modules.
Optimally, the pallets of vertically packed panels are banded and extra secured with protections between the panels with no space left so that they cannot move.
Nevertheless, clients might still require to have the modules packed horizontally, in many cases to save costs and time during unpacking. In such cases, good buffer materials between each module and around the modules are necessary to reduce potential damages.
Additional help would be to create the modules, which however comes at higher shipping costs.
Dangers during loading and transport
With loading, transport and unloading there lie more dangers ahead: improperly packed, the mechanical stresses and risks the panels are exposed to during their long journey are multiple, therefore good packaging is essential to reduce the potential impacts of various, high probable factors that can occur during transport, such as rough handling during loading and unloading, walking on the pallets by workers, stress vibrations to the modules while being carried in a truck on a bumpy road, bouncing of badly-packed modules on a pallet while shipped via sea.
Damages on the modules may even occur at the factory even with good packaging of the panels. Many manufacturers see their part of the job (well) done once the modules are packaged and can be handed over to the forwarders and shipping companies.
Dangerous impact factors are not well taken into account and can already start when storing the packed panels in a warehouse or lifting them onto a truck.
Careless workers could with their forklifts easily damage the panels which end consumers may visually notice in form of dents on the pallet or in worse cases in form of underperforming cracked panels.
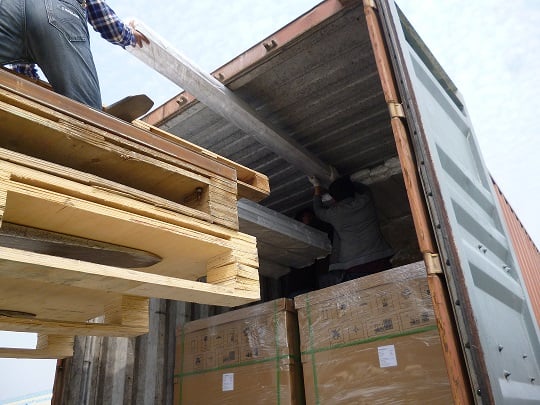
Loading of panels, walking on the pallet
Conclusion
Correct, safe, and careful packaging of solar panels is becoming an increasing issue in an industry in which many companies compete against each other with similar products and pricing plays a crucial role.
There already exist some companies specializing in solar (PV) module packaging, offering advanced packaging materials and sound packaging solutions.
There will be global standards at a certain point in time to which more and more manufacturers will adhere. Until then, when importing solar panels overseas, make sure at multiple steps from the purchase, packaging, loading, transport, to the arrival and unloading that your panels are packed safely and handled cautiously.
Geoffrey Kaila
on 06 Oct 2022Bob Turnage
on 31 Mar 2020Jessie Angelaere
on 25 Jun 2015Marcus
on 22 May 2014