Small components have a big impact
Stäubli is the manufacturer of the original MC4 connector and holds nearly 50% of the global market share. With the current global yearly production of solar modules standing at about 100GW, it also means that every year there are about 50GW of solar modules coming onto the market that feature non-original connectors. Our team of quality engineers at Sinovoltaics observes on a daily basis the various connectors used at the PV factories in Asia, and we deem it important for PV project developers to understand the importance of using original connectors.
In the article we discuss MC4 connectors, the role company Stäubli is playing in the connector market, and the risk of using ‘MC4 compatible’ alternatives.
This article is an extract from the Webinar that Sinovoltaics hosted together with Stäubli on 17 September 2020. You can re-watch the Webinar by clicking on the link below:
—>> Re-watch the Webinar featuring Stäubli discussing the latest trends in Solar Cabling and MC4 Connectors
Stäubli, the manufacturer of the original MC4 connector
Stäubli is a Swiss, family-owned company founded in 1892 and has three main divisions: textile machinery, robotics products and connectors. The company employs approximately 6,000 people. Stäubli has a substantial market share of roughly 50% in the PV connector industry. As of today the company has 300 GW+ of PV projects connected with their MC4 connectors. The company aims to more than double its production capacity by the end of 2021. Their key focus is on bankability, following the trend for developers to utilise quality components to get their projects financed.
Stäubli invented the first PV connector back in 1996. MC stands for Multi Contact and 4 stands for 4 millimetre because the conductor cross section of this contact is 4 millimetre. These days Stäubli produces connectors on three continents; Europe, North America, and China. Europe is their primary market – the company mainly produces for European projects and businesses, with North America and China housing secondary factories. All of the factories use exactly the same equipment; the same machines adhere to the same standards. This ensures that all connectors are of similar quality, no matter at which factory the connectors have been produced.
Stäubli fully owns all of its production equipment. To the contrary most of their competitors subcontract to other factories for injection, molding of parts, stamping of metal parts or other components. Subcontracting often leads to compromises in quality.
How to recognise original MC4 connectors
Many PV plant developers encounter problems with the so-called ‘MC4 compatible connectors’. And connectors seem to be a topic that few companies really think about. Some of our clients specifically ask the factory for the original MC4. However, there are plenty of buyers who don’t recognise the original MC4 connectors. Most buyers simply accept whatever connector comes with their solar modules.

Original Stäubli MC4 connector
What’s happening at the pv factories
During quality inspections at the PV factories, we see the Tier 1 factories use dozens of different connectors. While the original MC4 connectors are widely used, each manufacturer has alternative connectors on their certified CDF’s. This means factories can freely choose between multiple connector suppliers depending on availability.
Clients that only want the original MC4 connectors typically state this requirement specifically in their purchase contracts. Our team of quality engineers verifies during quality inspections if the right connectors have been used.
A selection of of connectors we spot at the factories in Asia. Can you spot the original MC4’s?
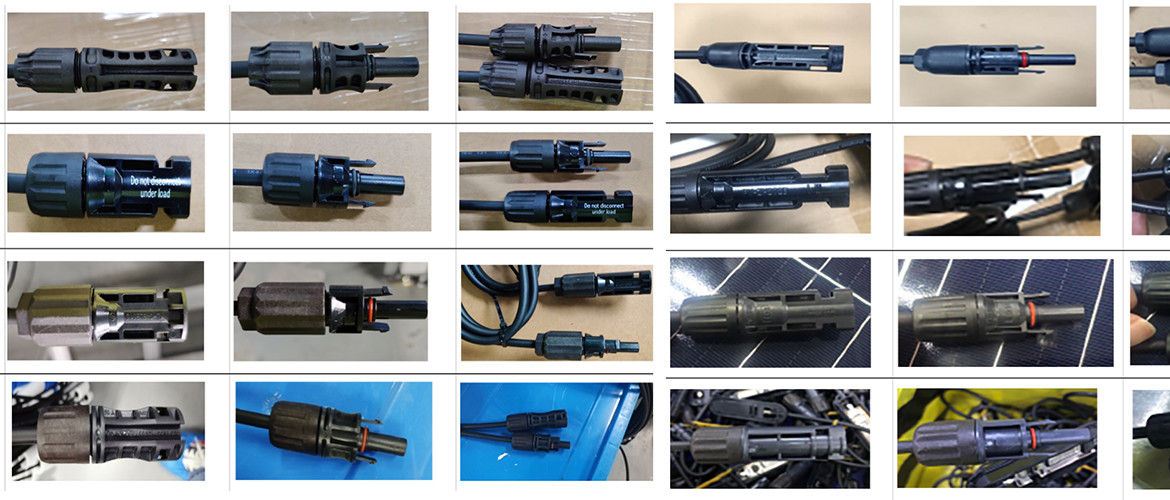
Various connectors spotted at the factories in Asia during quality inspections by team Sinovoltaics
Why use an original MC4 connector?
Unfortunately, people generally pay a lot of attention to solar modules and inverters, but not enough to cables and connectors. If you don’t know what connectors are built into the module or inverter, there’s a good chance that you’ll connect 2 different types of connectors. Connection different brands of types of connectors may lead to problems. This eBoS failure is your cost at the end of the day. So the question is how do you balance the CAPEX at the beginning of the project development with the potential OPEX you might have afterwards. Picking the right components will dramatically impact the profitability and LCOE.
To demonstrate this issue we normally use an example of the importance of tires on a car. Would you accept an unknown brand of tires for your car? Mismatching brands of tires on a car? Definitely not a good idea. A tire is a safety element and the connectors play a similar role. So while you can spend a lot of time selecting the right model and latest technology, you will likely end up with a lot of issues if you don’t pay the same attention to cables and connectors. All the energy produced goes through connectors. A connector is a small pieces of plastic with a conductive core – and we expect this to function for 25+ years.
Example 12MW project: ‘MC4 compatible connectors’ with cross-connection issues
Recently we’ve seen several cases where connectors had a significant impact on the performance of PV plants. One particular case was a 12 megawatt project in Western Europe. The modules were supplied by a Tier 1 factory from China and the solar modules were sitting in a warehouse in the Netherlands. They were due to be shipped to the construction site within a week. Suddenly the Tier 1 factory emailed the developer to explain that the modules they had sent over came with two different types of connectors. Those ‘MC4 compatible’ connectors could not be used together (!). In other words, these modules were of the exact same brand and model, but couldn’t be connected. A cross connection between the two brands of connectors was deemed to be unsafe and could lead to performance issues in the future.
A Tier 1 module brand using multiple connector brands
Where did things go sideways? Half of the 12MW order had been produced by the Tier 1’s own factory, while the other 6MW came from an OEM factory. This is a very common practice because all major factories work with multiple OEM factories. The OEM in this case used different junction boxes and different connectors than the main factory.
Of course the developers wasn’t to blame. However if the developer had connected these modules, the factory would have voided the product and performance warranty. After all, they had given a warning that these connectors cannot be used together.
This issue led to a logistical challenge to ensure a successful installation of these modules. The EPC had to install six megawatts of modules at one side of the field with one type of connector. At the other side of the field, they had another six megawatts of modules, with the different type of connector. That’s a lot of hassle to reduce the risk of a cross connection!
How about testing ‘compatibility’ between various connectors?
What’s interesting is that we spoke to one of the Certification Bodies about this topic and enquired whether they could simply test two different types of connectors? For instance, if you have a connector from Brand A and one from Brand B, isn’t there a test that can be done to determine if the two will work together successfully? The Certification Body replied they do not offer such a test, as from their experience the risk is too high that overheating and underperformance will occur in the long-run.
How often do cross-connections happen?
Cross-connection is a very common problem. In Europe, well trained EPCs or project developers, and owners dedicate a lot of time to this issue in an effort to eliminate the problem.
Stäubli MULTILAM technology
Disclaimer, promotional content! 😉
MULTILAM is Stäubli’s core technology that ensures good connection with low contact resistance.
How does the Stäubli Multilam technology work?
Nowadays PV projects are expected to function for well over 25 years. MULTILAM has been designed with the aging process in mind, and adjusts according to day and nighttime temperatures. Competitors copying the MC4 have also tried to develop the MULTILAM, but so far none have had success.
Staubli claims that its Multilam technology provides a constant spring pressure with reliable low contact resistance, and prevents the connectors from overheating:
Failures and their financial impact
Stäubli has been a part of a new initiative in Europe funded by the European Commission, called Solar Bankability.
The EU-funded Solar Bankability Project aims to establish a common practice for professional risk assessment on the basis of existing studies and collected statistical data of failures in PV plants. Its risk analysis tends to assess the economic impact of technical risks and how this can influence various business models and the LCOE. In a first attempt, the project presents a cost-based Failure Modes and Effects Analysis (FMEA) to be implemented into the PV sector and tries to define a methodology for the estimation of economic losses due to planning failures, system downtime and substitution/repair of components (Source: Staubli)
The Solar Bankability project looks at the top 20 technical failures and potential impacts on cost. Solar cabling and connectors are estimated to be one of the major causes of economic losses:
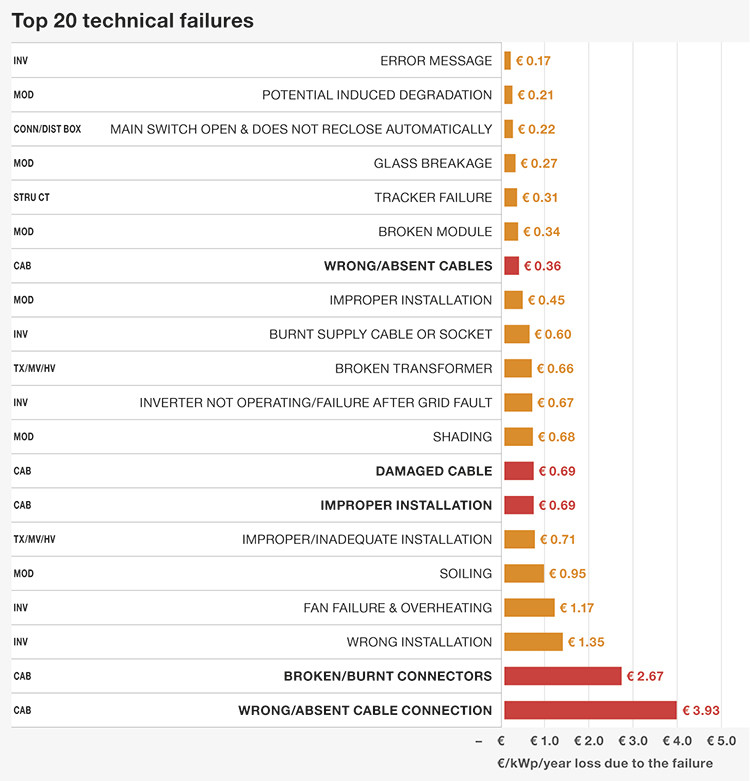
Calculation of the economic impact: Solar Bankability is a project funded by the European Commission’s Horizon 2020 program www.solarbankability.org
Price difference original Stäubli MC4 connectors and alternatives
On the total initial cost of your project, the cost for cabling is close to 1%. When we look at connectors alone, it’s only 0,003% of total CAPEX. Looking at the price difference between connectors, it is clear that the power industry and all of its key players are under tremendous pressure to keep working on cost reduction and reducing overall price.
Even with a 20-30% price difference between a cheap manufacturer and Stäubli the potential initial savings is really small. Especially when considering product performance, safety, the potential loss in electricity production and the impact on the OEM cost.
Are there approved compatible alternatives, or certified list of connectors?
It is important for the industry to understand that the word “compatible” is not appropriate because even if the connectors work together, and we assume they are compatible, in the long-run cross-connections cause damage to the plant and therefore inspectors and certification bodies won’t approve it. There are various risks associated with cross-connections, like higher resistance, increased chance of fire and underperformance. Furthermore, connectors used in different weather conditions have different requirements, like being close to the sea with humid and salty air, or in the dry desert area, or operating in high wind.
There’s no ‘certified list’ of connectors that properly work together. To reduce any risk, team Sinovoltaics recommends to always stick to one type of connector, never mix different types of connectors even when they’re named ‘MC4 compatible’ and preferably choose for the one and only original product in the market.. the Stäubli MC4 connector.