In part 1 of our solar panels in deserts series, we addressed the potentials and challenges for solar power in desert environments, with a special focus on hot deserts.
Despite the manifold challenges, interest in efficiently using the otherwise largely ‘useless’ deserts is very high and logic, which is mirrored by the increasing plant constructions all over our globe’s deserts, recently with Morocco taking the lead in desert solar projects.
When going solar in such extreme environments, standard crystalline-silicon modules are subject to enormous climatic and mechanical stress that put downward pressure on performance, yield, and thus project ROI in the long run. Fortunately, there are alternatives, such as concentrated solar power.
So, what technologies are available to cope with these challenging stress factors? And how to properly operate and maintain the modules in desert projects?
Solar power technologies for desert environments
The majority of existing solar power projects in deserts all over the world do not employ traditional crystalline-silicon or amorphous silicon modules, but concentrated solar power (CSP).
Concentrated solar power systems generate electricity by concentrating sunlight on a focal point or line which is then heated up and drives a turbine linked to a power generator.
Concentrated solar power is often confused with concentrator photovoltaics (CPV), which however directly converts the incoming sunlight into electricity using the photovoltaic effect.
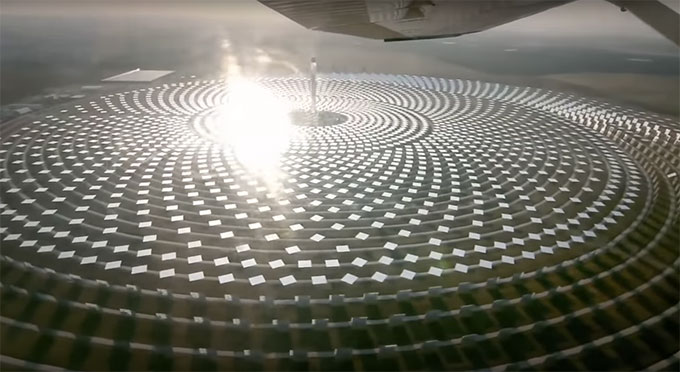
Concentrated solar power
Concentrated Solar Power Technologies
Concentrated solar power offers enormous advantages as compared to the classic PV mainstream. There are four major commercial CSP technology types which are:
1. Parabolic Trough: these are concentrated solar power collectors shaped like a parabola on both ends of the collector and usually oriented toward the sun at its yield-optimal average position.
With the sky-crossing of the sun throughout the day, the parabola-shaped collectors manage to catch sun arrays throughout the day that are then reflected a focal point along the dimpled middle line between the parabolic ends, the so-called absorber tube.
This straight tube contains a working fluid (or: medium) such as oil that is then heated up by the concentrated sun and produces steam that drives a turbine, subsequently producing electricity.
2. Dish Sterling: these are independently operating, parabola-shaped reflectors that consist of several modules constituting that large parabola, the so-called dishes.
Mounted on a solar tracking system, it tracks the sun during its crossing of the sky over the day and concentrates sunlight on a focal point. In doing so, the integrated working fluid is heated and then used to generate power using a sterling engine, which is a heat engine that works by cyclic expansion and compression of the working fluid at varying temperatures.
3. Power Tower: these are the more prominent types of concentrated solar power systems illustrated in media. Basically, the Concentrated Solar Power Tower Systems consist of concentrated solar power mirrors (heliostats) installed around a solar power tower on which the incoming solar energy is concentrated, creating significantly more heat.
These heliostats are often mounted on tracking systems that track the sun’s movement and thus optimize the performance efficiency of the heliostats.
4. Fresnel Reflectors: this type of concentrated solar power uses highly efficient fresnel lenses. Essentially, mirror segments concentrate the sunlight on a common absorber tube focal point which contains a working fluid.
The high sunlight concentration heats up the working fluid which then goes through a heat exchanger and then powers an engine to generate power.
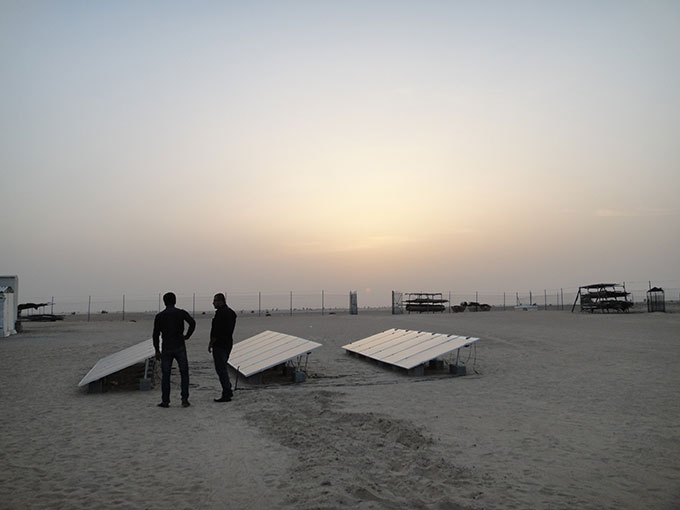
Solar panels in the Dubai desert
Photovoltaic Technologies
On the classic photovoltaic front, too, there have been efforts to produce and optimize modules capable of coping long-term with the harsh working environment of hot deserts, though these improvements have mostly come in form of material composition changes and material quality and less due to advances in structural designs.
There have been few exceptions however in recent years with module designs that include original concepts such as air ducts integrated with the modules that use the natural wind to improve cell cooling, though further research remains to be done.
Some module manufacturers have run operational and/ or comparison tests in deserts to analyze the performance of their modules and make improvements where possible. Similarly, solar project developers and investors have an interest in such tests before making further procurement decisions, involving specialized quality and comparison testing such as from our team at Sinovoltaics.
Especially in desert environments, using concentrated photovoltaic (CPV) technology can have some advantages over regular c-Si mono- / polycrystalline and thin-film technologies:
- Less solar cell material is required to capture the same or even more amount of radiation as a non-concentrating energy system. High-efficiency multi-junction cells are more expensive than standard Si solar cells, however, due to sunlight concentration, they require only a small cell surface.
- The entire system can be cost-effective due to fewer cell materials, low-cost optics, and increased output
A popular CPV type is Heliostat Concentrator Photovoltaic (HCPV). Similar to the working principle of some CSP technologies, HCPV uses large areas of lenses or mirror collectors (heliostats) to focus and beam sunlight in highly concentrated form to a small area of solar cells. The concentrated light is then directly converted by the solar cells into electric power. Further performance increases are possible when coupling HCPV with solar tracking systems.
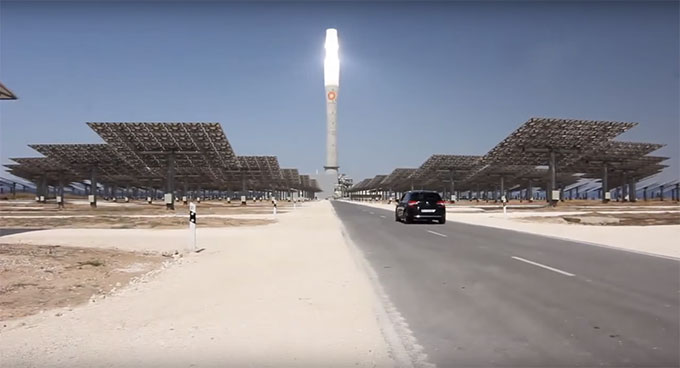
Concentrated solar power
Challenges to concentrated solar power and photovoltaic modules in deserts
As outlined in the previous part 1, the challenges to solar power systems are manifold in hot, mild, and even cold desserts:
- efficiency losses due to high temperatures, especially for modules with high negative temperature coefficients
- failing adhesion of encapsulant and back sheet triggered by high temperature
- abrasion due to often sharp sand grains blown over the module
- erosion of the mirrors in concentrated solar power systems due to sand and dust
- sand and dust which in small quantities – and in case of the rather transparent dust much larger quantities – are hardly visible but sufficiently nasty sun-blocking layers on the modules, bringing down output performance as well as that of the string in which it is located – even a few grams on a square meter can cause double-digit performance losses. Moreover, shading due to sand and dust layers can potentially trigger hot spots, which are particularly dangerous under high irradiance conditions in desert environments
- in some desert environments, even large size stones could be blown around and hit the modules and thus break the glass, frame, back sheet, electrical connections, and so on
- in cold deserts: humidity freeze risks that can render the module useless
These challenges are geared to costly operations and maintenance issues in desert environments.
Operations and maintenance – limitations and technologies
In order to cope with the high temperatures in hot and mild deserts, proper as well as cost- and resource-intense cooling is required which is often done by using precious water.
Concentrated solar power plants require steady cooling in order to run efficiently. Since there are to date no affordable and effective dry cooling technologies available in the market, precious water remains the primary cooling medium applied.
In this regard, to save precious potable water, with many mild and hot deserts located close to oceans, solar desert plants coupled with solar desalination systems are an interesting design option.
The challenge is not only the cost of the water itself and its significant value in desert regions but also the transportation of it to the plants as well as the proper and most resource-efficient use of the water during cooling. Often, water is stored in wells and then pumped – in some cases over larger distances.
Yet, water is not only used for cooling but also for cleaning in order to keep off dust. While for CSP mirrors down tilting is currently the best method to cope with erosion risks, for PV modules there are more interesting possibilities…
Different from the challenge of cost- and resource-efficient dry cooling, there are viable alternatives to water-based cleaning of solar modules and mirrors in desert environments. These are:
- electrostatic cleaning: this cleaning system uses electrostatic force to remove dust and sand from the surface of solar PV modules, with a charge flowing over the module that literally repels the dust and sand grains out of the charge’s way towards the edges of the module.
As another example of the close relationship between space technology research and the solar industry, this technology has been originally developed by NASA for its Mars landrover missions, consumes close to nil extra power, and has in tests proven to clean about 90% of all dust and sand particles, making it a very interesting alternative to water cleaning. One potential challenge is however wet muddy clumps of sand in those rare cases when it rains, after which the electrostatic forces will not be strong enough to repel the much heavier sand and dust clusters. Therefore, the dust and sand should be removed before raining. Moreover, this cleaning technology is difficult to re-integrate with existing plants. - mechanical brushing: akin to the working principle of a toothbrush, these are waterless devices with an integrated brush that are mounted on a string of modules and run during cleaning along rails over the modules. One such system is the NOMADD (NO-water Mechanical Automated Dusting Device) developed at the King Abdullah University for Science and Technology (KAUST) in Saudi Arabia. NOMADD is an automatic and quite cost-efficient mechanical solar PV module cleaning device that can be integrated with the existing system and runs the brusher over a 200m long x 5m wide string of modules, capable to clean hundreds of Megawatts in less than an hour.