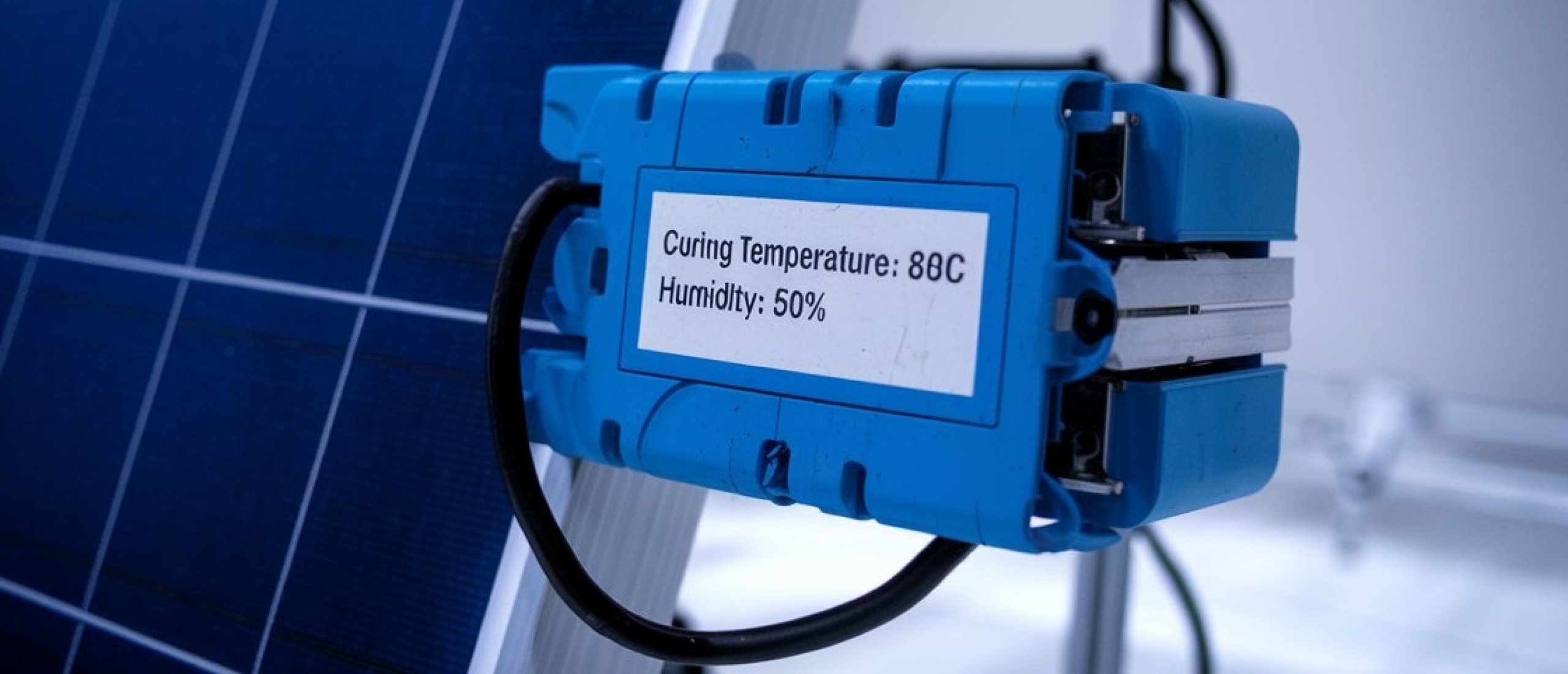
The Role of Curing Temperature and Humidity in Preventing Junction Box Delamination and Frame Looseness in Solar PV Modules
In the manufacturing of solar photovoltaic (PV) modules, ensuring the durability and reliability of each component is paramount. Two critical issues that can compromise module performance are junction box delamination and frame looseness. Both are closely linked to the curing process, particularly the control of temperature and humidity. This blog delves into the importance of maintaining optimal curing conditions and their impact on the long-term integrity of solar PV modules.
Frequency and impact of Junction Box Delamination and Frame Looseness
According to studies published in journals such as Solar Energy Materials and Solar Cells and Progress in Photovoltaics and IEA PVPS reports and fields studies by IEEE, the incidence of junction box delamination & frame looseness can range from 5% to 20% in field-deployed modules after 5 to 10 years of operation. In particular in harsh climate conditions which can lead to mechanical instability, electrical failures and moisture ingress; all in all impact yield.
Understanding the Curing Process
The curing process is an essential stage in solar PV module manufacturing. It involves the chemical and physical stabilization of adhesives, encapsulants, and sealants used to bond various components, such as the junction box, frame, and glass. Proper curing ensures strong adhesion, reduces the likelihood of material degradation, and enhances the overall structural integrity of the module.
Impact on Junction Box Delamination
The junction box is a critical component that houses the electrical connections of a solar module. Delamination of the junction box can lead to serious issues, including moisture ingress, electrical failures, and even safety hazards. Improper curing, particularly under suboptimal temperature and humidity conditions, is a leading cause of junction box delamination.
1. Temperature Control: Curing at a temperature that is too low can result in incomplete cross-linking of adhesives, leading to weak bonding. Conversely, excessively high curing temperatures may cause thermal stresses, which can weaken the bond over time.
2. Humidity Levels: High humidity during curing can interfere with the adhesive’s ability to form a robust bond. Moisture can also get trapped between layers, causing delamination when the module is exposed to environmental stressors such as thermal cycling or UV exposure.
Impact on Frame Looseness
The aluminium frame of a solar PV module provides structural support and facilitates secure mounting. Frame looseness not only affects the module's mechanical stability but also increases the risk of water ingress and potential damage to the encapsulant and internal layers.
1. Temperature Fluctuations: Inadequate curing temperatures may lead to insufficient expansion and contraction of the adhesive, resulting in poor bonding between the frame and the glass or backsheet. This can manifest as frame looseness over time.
2. Controlled Humidity: Excessive humidity during curing can weaken the adhesion between the frame and the module’s edges, making it more susceptible to loosening under mechanical stress.
Best Practices for Curing
To mitigate the risks of junction box delamination and frame looseness, the following best practices should be observed during the curing process:
1. Optimize Curing Temperature: Maintain a consistent temperature within the recommended range specified by adhesive and sealant manufacturers. Regular calibration of curing ovens is essential to avoid temperature fluctuations.
2. Monitor Humidity Levels: Use dehumidifiers or climate-controlled curing chambers to maintain ideal humidity levels, typically below 60%. This helps prevent moisture interference during the curing process.
3. Implement Quality Control: Conduct routine adhesion tests and visual inspections to identify any potential delamination or frame loosening early in the production process.
4. Invest in Advanced Curing Technologies: Technologies such as infrared or UV curing can offer precise control over temperature and curing time, improving bond strength and overall module reliability.
Sinovoltaics Monitoring of Temperature & Humidity of Curing Rooms
Knowing the importance of how temperature and humidity impact frame looseness and junction box delamination in the first 5 - 10 years; the team monitors the temperature & humidity in the curing room. Revising those with requirements noted in the curing and silicon material suppliers.
Conclusion
Maintaining optimal curing temperature and humidity is crucial for ensuring the long-term reliability of solar PV modules. By prioritizing these factors, manufacturers can significantly reduce the risks of junction box delamination and frame looseness, delivering high-quality products that withstand environmental challenges and maximize energy yield. Sinovoltaics monitoring of temperature and humidity of the curing room can help mitigate common field failures in the first 5 - 10 years. A commitment to stringent curing practices not only enhances product durability but also reinforces the trust and satisfaction of customers in the growing solar energy market. For more information, contact Sinovoltaics.