Sinovoltaics explains the the production cycle of solar PV modules from pieces of raw material to the final electricity-generating panel. This article will provide some basic details and knowledge about solar panel production to give you a better understanding of what you are actually buying, specifically looking at the creation of traditional silicon-based solar panels.
Solar panel production
Getting raw material for the solar cell
Solar cells basically consist of pure silicon, a metalloid which in nature is not available in that pure condition. A first step is the deoxidization of silicon dioxide (SiO2) through carbon arc welding (CAW). In this process, carbon dioxide (CO2) and silicon are produced. This silicon produce with ca. 99% still not sufficiently pure for solar cells must then further be purified. Purification is done through the floating zone technique under which the 99% silicon rods are moved through a heated zone many times into the same direction until all the impure parts of the rod are at one end of the silicon rod. The impure part is then cut off and the remaining 100% pure silicon rod can now be used in the production process.
Making the solar cell
Crystal seeds of the silicon a in the so called Czochralski process put into melted polycrystalline silicon for further purification and processed with the puller into cylindrical silicon ingots (for monocrystaline cells) or with the dss furnace into quadratic silicon blocks (for polycrystalline cells). These ingots are then – depending on the geometrical shape requirements – with a wiresaw sliced into silicon wafers that are – depending on the production purpose – either monocrystalline or polycrstyalline cells.
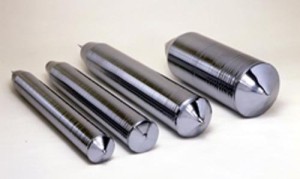
Silicon ingots that can be sliced into wafers
With a diffusion machine boron and phosphorus are added. Now electrical contacts are placed to connect each solar cell to another as well as to the junction box. The thinner the electrical contacts are the more sun can be absorbed by the cell so the contacts must be very thin. After this, tin-coated copper strips are placed between the cells. Since pure silicon is still to shiny and can reflect up to one third of the sunlight, anti-reflective coating of titanium dioxide or silicon oxide are put on the cell.
Framing the cells to a whole module and testing
After these steps, the solar cells are then commonly sealed into ethylene vinyl acetate, put into an frame that is sealed with silicon glue and covered with a mylar back on the backside and a glass or plastic cover on the frontside. Before the ready panel can be sold it must sustain a testing procedure to ensure its quality. Apart from a visual test of the panel, the testing included a flash test that measures the open-circuit voltage (VOC), voltage at maximum power point (VMP), short-cirucit current (ISC), current at maximum power point (Imp), maximum power (Pm (W)) and the fill factor (FF). The parameters of the modules are measured at standard test conditions (STC). STC specifies a temperature of 25 °C and an radiance of 1000 W/m2 with an air mass 1.5 (AM1.5) spectrum. These correspond to the radiance and spectrum of sunlight incident on a clear day upon a sun-facing 37°-tilted surface with the sun at an angle of 41.81° above the horizon. This condition approximately represents solar noon near the spring and autumn equinoxes in the continental United States with surface of the cell aimed directly at the sun.
Why additional external quality control?
After the tests are successfully passed, the panels are ready for sale. However, quality deficiencies and malfunction can often be found in the final product, even from renown manufacturers. This is due to the complicated production procedure that requires close attention. In this complicated process and rush production times, minor deficiencies or defects are sometimes not avoidable if there is no large quality control department within the solar company. This is why quality testing from external auditors and PV experts has increasingly become important in recent years, in particular for customers who order panels in far-away countries like China and have no possibility to fly-over to check the panels.
Solar panel quality inspections
Are you purchasing solar panels, inverters or mounting racks in the Greater China region? Sinovoltaics performs independent quality inspections on-site at solar manufacturers.
Advantages:
- Replace defects prior to shipment
- Independent testing report
- 100% certainty about product quality
- International testing crew specialized in solar PV panels, inverters and mounting racks
Learn more about Sinovoltaics and its PV quality inspection and consultancy services
Ravi Lanjewar
on 29 Jan 2018Ravikumar
on 14 Oct 2017