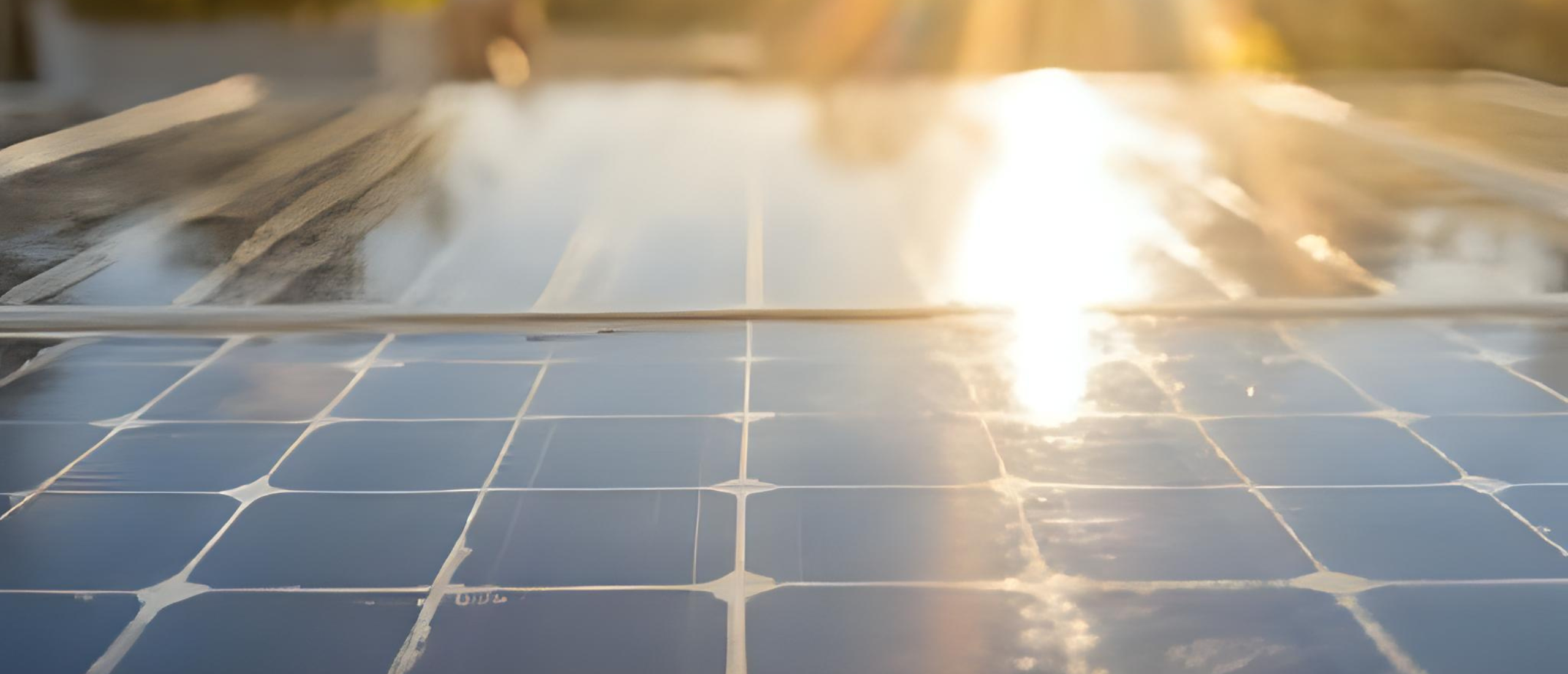
Heterojunction Technology (HJT): What It Is and Why It Matters for Solar Panel Quality
Introduction
As the solar industry pushes for higher efficiency and longer-lasting photovoltaic (PV) modules, Heterojunction Technology (HJT) has emerged as a leading innovation. Originally developed by Sanyo in the 1980s, HJT has gained new momentum in recent years thanks to its superior performance characteristics—especially in high-temperature environments and under low-light conditions.
But high-tech doesn’t always mean high-quality. That’s why understanding the manufacturing nuances of HJT panels is essential—not just for manufacturers and EPCs, but also for investors, asset owners, and quality assurance professionals. At Sinovoltaics, we see HJT as a major advancement—but also one that demands robust quality control inspection and auditing protocols to ensure it lives up to its promise.
What Is Heterojunction Technology (HJT)?
Heterojunction Technology is a hybrid solar cell structure that combines crystalline silicon (c-Si) with amorphous silicon (a-Si) layers. More specifically, HJT solar cells are composed of:
- A crystalline silicon wafer (typically n-type)
- An intrinsic amorphous silicon layer
- Doped amorphous silicon layers (p-type and n-type)
- Transparent conductive oxide (TCO) layers
- Dual-sided metal contacts
This layered structure enables HJT cells to leverage the best of both silicon types—crystalline for high efficiency and amorphous for better surface passivation and lower recombination losses.
Key Benefits of HJT
- High Bifaciality: HJT modules can reach bifaciality factors of 90% or more.
- Low Degradation Rates: Better light-induced degradation (LID) and potential-induced degradation (PID) resistance (lower solar panel degradation rate).
- Superior Temperature Coefficient: Typically around -0.26%/°C, improving yield in hot climates.
- Enhanced Low-Light Performance: HJT cells generate more power during early morning, late evening, and cloudy days.
- Longer Lifespan: Thanks to reduced stress on materials and passivation layers there is an increased life cycle assessment of solar panels.
HJT in the Market: Trends and Outlook
Manufacturers such as LONGi, REC, and Huasun are scaling up HJT solar module production as global demand grows for ultra-high-efficiency solar modules. With module efficiencies surpassing 23% and potential for even higher gains with tandem cell structures, HJT is carving out a niche in premium residential, commercial, and utility-scale applications.
However, HJT production is capital-intensive and technically demanding. It requires precise temperature control, advanced deposition techniques, and careful handling of materials to avoid defects such as pinholes, TCO delamination, and contamination of the a-Si layers.
Why HJT Demands Specialized Quality Control Inspections
While HJT offers compelling advantages, its complexity raises the bar for quality assurance and factory auditing. At Sinovoltaics, our inspection teams have observed several HJT-specific issues that can compromise long-term performance:
Common HJT Manufacturing Challenges
1. Temperature Sensitivity of a-Si:H Layers
- Issue: The intrinsic and doped amorphous silicon layers degrade under high thermal stress. Temperatures above ~200°C can cause hydrogen effusion and microstructural changes, compromising passivation.
- Implication: Module processing must avoid high-temperature steps, limiting metallization options and complicating lamination.
- Mitigation:
- Use of low-temperature curing silver pastes.
- Strict control of lamination temperatures (~150°C max).
- Exclude high-temp soldering in module assembly.
2. TCO Degradation
Issue: The transparent conductive oxide (TCO) layers used in HJT (typically ITO or ZnO:Al) can degrade under environmental stress (e.g., damp heat, UV).
Implication:
a. Loss of conductivity and optical transmission over time.
b. Increased series resistance, leading to power loss.
Mitigation: Use of stable, high-purity TCOs and robust encapsulants; inclusion of edge sealant to prevent moisture ingress.
3. Light-Induced Degradation in a-Si:H
Issue: While the crystalline core of HJT cells is LID-free, the amorphous silicon layers can suffer from Staebler–Wronski effect, a light-induced metastable defect formation typical of a-Si:H.
Implication: Slight degradation in Voc and FF during early operation.
Mitigation:
- Optimizing a-Si:H layer thickness and hydrogen content.
- Use of bifacial designs to average light exposure and thermal annealing effects.
4. Metallization Challenges
Issue: HJT requires low-temperature metallization (e.g., <200°C), often using silver pastes with limited adhesion and contact stability.
Implication:
- Risk of delamination or contact corrosion under thermal cycling or damp heat.
- High cost due to thick Ag fingers (no current screen-printed aluminum option).
Mitigation:
- Use of plated copper metallization (SmartWire or busbarless interconnection).
- Encapsulation designs that reinforce mechanical bonding.
5. Encapsulation-Induced Degradation
Issue: EVA encapsulants may cause yellowing and degradation of the TCO/a-Si:H layers under UV exposure and heat.
Implication: Loss of optical performance and passivation.
Mitigation: Use of UV-stable POE or dual-glass configurations to minimize UV damage and water ingress.
6. Bifaciality and Rear-Side Reliability
Issue: HJT cells are naturally bifacial (up to 90% bifaciality), but rear-side degradation mechanisms—especially UV-induced changes in a-Si:H layers—remain a concern.
Implication: Power loss and passivation degradation on the rear under bifacial exposure.
Mitigation
- UV-filtering encapsulants.
- Extensive rear-side light-soaking and stress testing.
7. Potential-Induced Degradation (PID)
Issue: HJT is less prone to traditional PID-p (polarization) due to n-type wafers, but may be susceptible to PID-s (shunting) due to high surface fields.
Implication: Shunting through TCO/encapsulant interfaces under high voltage bias and humidity.
Mitigation: Robust glass-glass encapsulation, and PID testing under IEC TS 62804-1-1.
8. UV- and Damp Heat Sensitivity of a-Si:H/TCO Stack
Issue: The interface between a-Si:H and TCO layers is sensitive to UV-driven bond breaking and moisture ingress, especially in humid climates or near salt-mist environments.
Implication: Decreased shunt resistance, increased recombination, and contact instability.
Mitigation: IEC 61215 extended damp-heat and UV tests; salt mist (IEC 61701) and ammonia (IEC 62716) for coastal/agricultural applications.
9. Glass-Glass Bifacial Configuration Risks
Issue: Mechanical rigidity of glass-glass increases risk of microcracks during transport and installation, especially with thinner wafers (e.g., <150 μm).
Implication: Long-term reliability degradation due to crack propagation and hotspot formation.
Mitigation: BOM validation, robust framing, and handling protocols during logistics.
10. Manufacturing Yield and Uniformity Issues
Issue: HJT has tight process tolerances, especially for:
- a-Si:H layer thickness and uniformity.
- TCO conductivity and transparency.
- Ag paste firing profile.
Implication: Cell-to-cell variation, unpredictable degradation rates, and module mismatch.
Mitigation: Strict inline QA, advanced monitoring (PL/EL imaging), and tight process integration.
These are not your average solar panel issues. That’s why our factory audits for HJT production focus heavily on testing solar panels:
- Cleanroom protocols and contamination controls
- PECVD (plasma-enhanced chemical vapor deposition) equipment calibration
- TCO sputtering process checks
- Bifaciality and thermal stress testing
- Cell-to-module (CTM) loss analysis
TOPCON vs HJT/SHJ
Field Performance vs. Lab Test Specs: The Inspection Imperative
One of the biggest misconceptions about HJT is that lab-rated specs equal field performance. While HJT modules boast impressive datasheet numbers, real-world performance hinges on manufacturing consistency and supply chain quality.
For example, inconsistencies in the silver paste or substandard interconnection ribbons can impact thermal cycling resilience, ultimately affecting the module's performance over time.
At Sinovoltaics, we stress the importance of third-party validation during:
- Pre-shipment inspections (quality control inspections)
- Container loading supervision
- Batch-level flash testing and EL imaging
- Bill of Materials (BoM) verification
This approach ensures that what you expect from your HJT modules aligns with what you actually receive—reducing the risk of warranty claims, performance shortfalls, or worse, systemic project losses.
Conclusion: High-Tech Modules Need High-Caliber Oversight
Heterojunction Technology represents a leap forward in solar efficiency and durability, but that leap comes with greater complexity and risk. Whether you're an EPC selecting modules for a high-irradiance site or a financier assessing long-term yield, understanding the critical role of solar inspection services and quality assurance is essential.
At Sinovoltaics, our experience auditing HJT manufacturing lines across Asia has shown us one thing clearly: premium or new solar cell technology still needs rigorous verification against established quality control standards.
If you’re investing in HJT modules, make sure your quality processes are as advanced as the technology itself.
Want to ensure your HJT modules deliver top-tier performance?
Reach out to Sinovoltaics for comprehensive factory audits and inspection services tailored to next-gen solar PV panel technologies.